Deployable Tensegrity Structures with Inflatable Compression Struts
Deployable Structures Research Project
Atlanta, GA
2018
Collaborators:
Michael Koliner, Chris Putman, Vinay Teja Meda, and Jim Case

![]()
![]()
![]()
![]()
The research leading to this preliminary proposal has been centered around developing material schemas for high-performance air-struts. As the tensegrity structure is loaded, the inflated compression struts tend to deform and buckle. Our investigation has been focused on developing strategies for buckling resistance in these low-pressure struts. The inflated portion of the strut serves put a series of steel cables in tension, which provide the member with its stiffness. Through several phases of physical prototyping, we have developed several material schemas of inflatable air struts for small-scale tensegrity structures (up to 2 cubic meters) using widely available materials such as polymeric tubing, PVC pipe caps and steel cables. As this work is on-going, our team is currently developing our next experiments will lead to strategy we are proposing for the exhibition.
The proposed pavilion seeks to extend the concept of inflatable tensegrity structures by physically demonstrating it at large scale - within the spatial limits of the exhibition guidelines of 4m x 4m x 4m. The structure will demonstrate how combining the advantages of tensegrity and pneumatic structures results in a minimum weight structure that maximizes its global volume change before and after it is deployed. The design is intentionally simple: a 4-strut tensegrity geometry is used as the base form of the pavilion to demonstrate the precision of the system and the effectiveness of the low-pressure cable-stabilized struts. Whereas our previous prototypes used relatively weak plastic tubing, the struts used for the pavilion will be made of much stiffer (though still semi-transparent) membrane material. The tension cable scheme will also incorporate new strategies based on insight we gathered from recent analysis and laboratory testing. The pavilion will have integrated lighting and air-control systems in the actuating end caps of the struts; authoring them with different lighting schemes. Our submitted paper will discuss the pavilion and the numerous scale prototypes that precede it, present testing results and analytical strategies for the struts, and speculate on the range of applications for this technology.
Woven Nylon + PVC + Tension Cable Compression Strut with System - April 2019
![]()
![]()
Woven Nylon + PVC + Tension Cable Compression Strut with System - April 2019
![]()
HDPE Compression Strut with Tension Cable System - December 2018
4-Strut Prototype // HDPE Membranes - October 2018
![]()
![]()
3-Strut Prototype // HDPE Membranes - September 2018
![]()
![]()
Proof of Concept Prototype // Rubber Bike Innertubes - August 2018
![]()
Other Projects:
Abstract:
This pavilion proposal for the WG21 lightweight pavilion exhibition consists a free-standing structure that extends the principles of active-deployed tensegrity structures through the use of inflatable compression struts. Replacing rigid compression struts traditionally found in tensegrity structures with air-struts presents the opportunity to minimize the overall weight and maximize the global volume change of the structure. Previous deployable tensegrity structures have used external actuation and rigid materials for compression elements, resulting in a limited shape-change capacity. Some proposals for inflatable tensegrity systems in aerospace engineering have been made through small-scale prototype models (less than 1 cubic meter) that use continuous airflow systems. Others have developed analytical and numerical deployment simulation models for such systems and proved it was possible at large scales, but not physically tested.
Link to the full paper “Self-Deploying Tensegrity Structures with Inflatable Struts” (IASS 2019)
Link to the full paper “Deployable Tensegrity Structures using Pneumatic Compression Members” (S-Arch 2019)
This pavilion proposal for the WG21 lightweight pavilion exhibition consists a free-standing structure that extends the principles of active-deployed tensegrity structures through the use of inflatable compression struts. Replacing rigid compression struts traditionally found in tensegrity structures with air-struts presents the opportunity to minimize the overall weight and maximize the global volume change of the structure. Previous deployable tensegrity structures have used external actuation and rigid materials for compression elements, resulting in a limited shape-change capacity. Some proposals for inflatable tensegrity systems in aerospace engineering have been made through small-scale prototype models (less than 1 cubic meter) that use continuous airflow systems. Others have developed analytical and numerical deployment simulation models for such systems and proved it was possible at large scales, but not physically tested.
Link to the full paper “Self-Deploying Tensegrity Structures with Inflatable Struts” (IASS 2019)
Link to the full paper “Deployable Tensegrity Structures using Pneumatic Compression Members” (S-Arch 2019)
Deployable Structures Research Project
Atlanta, GA
2018
Collaborators:
Michael Koliner, Chris Putman, Vinay Teja Meda, and Jim Case
4-Strut Prototype II
// PVC + Nylon + Steel Cable Reinforcing - May 2019

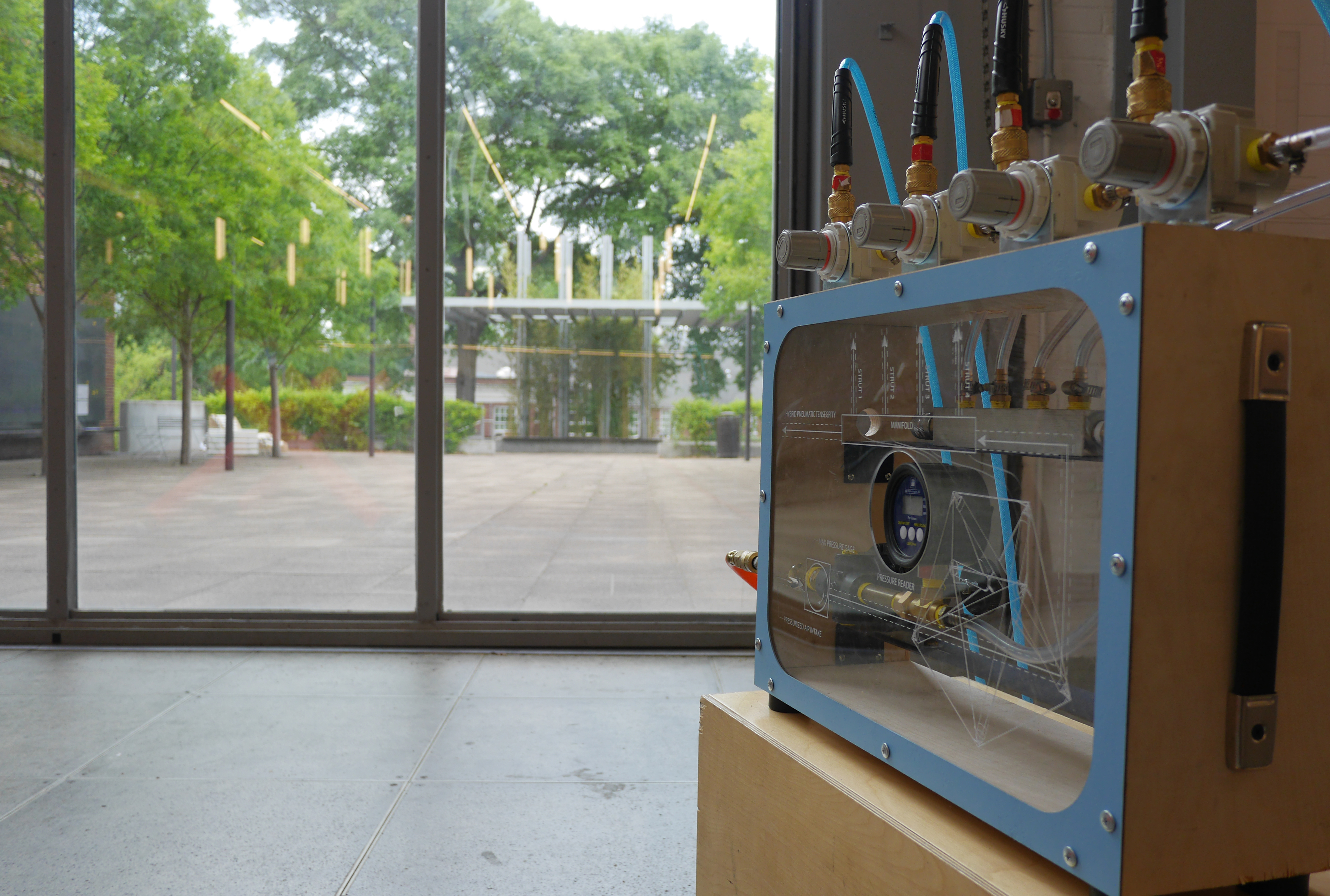
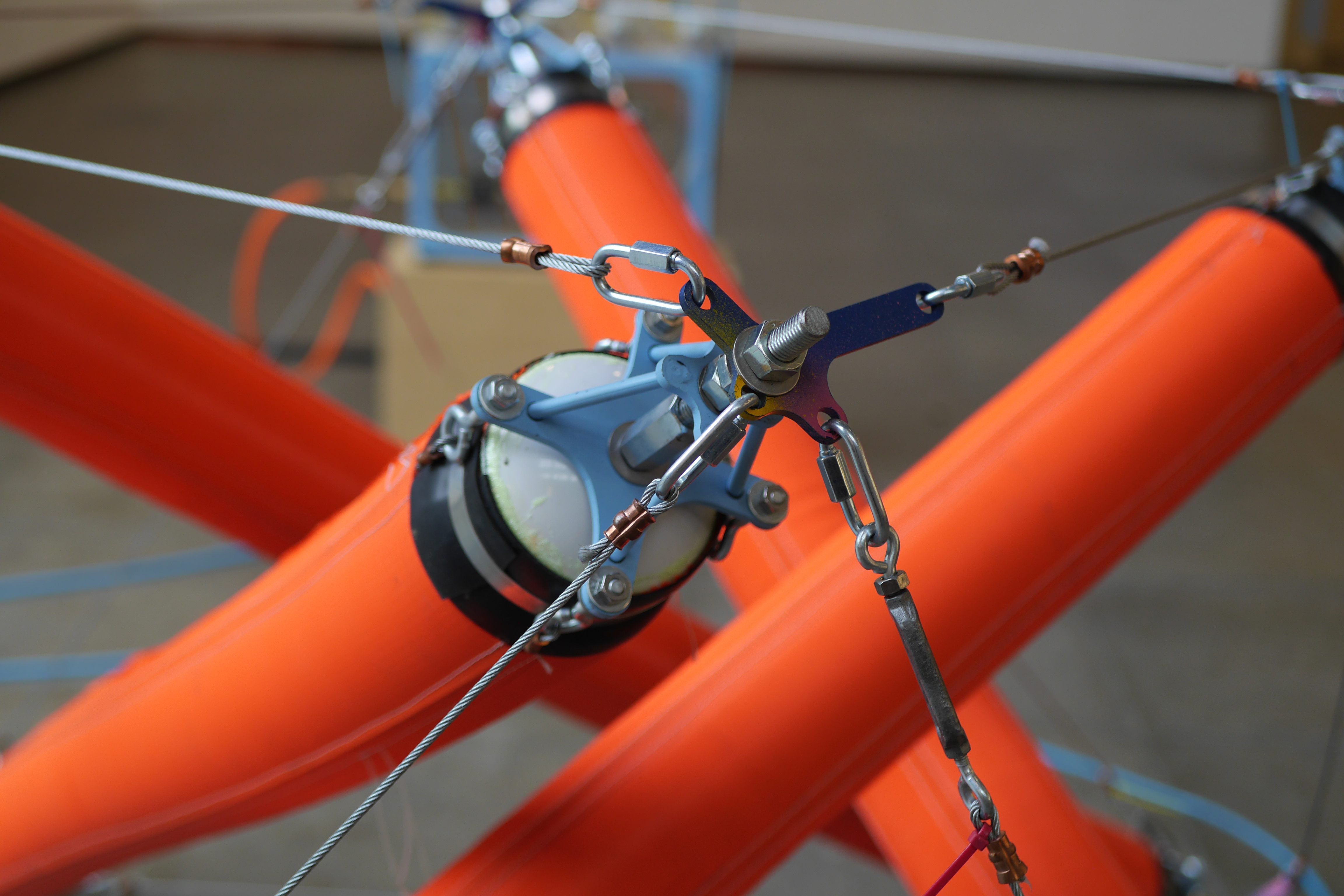
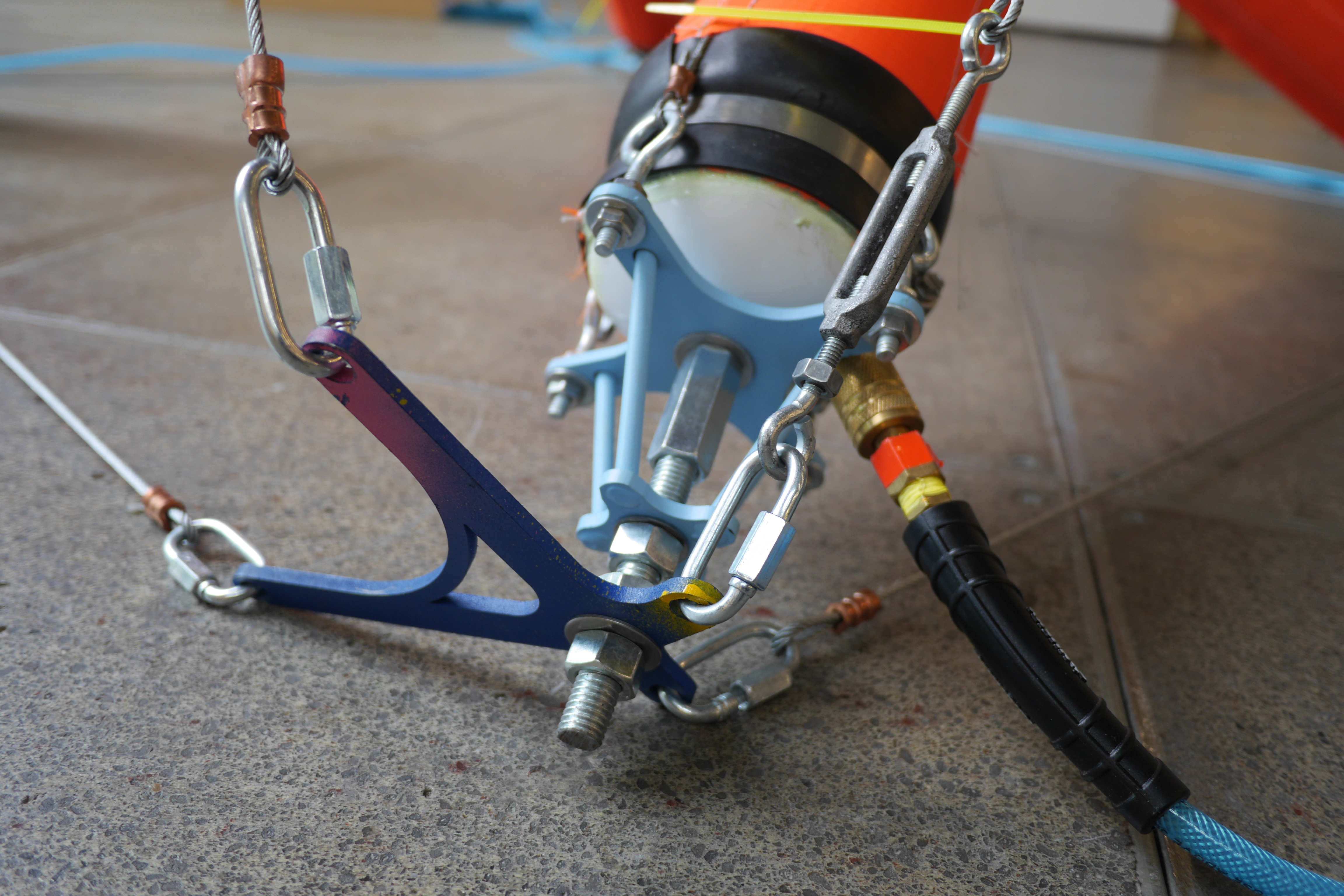
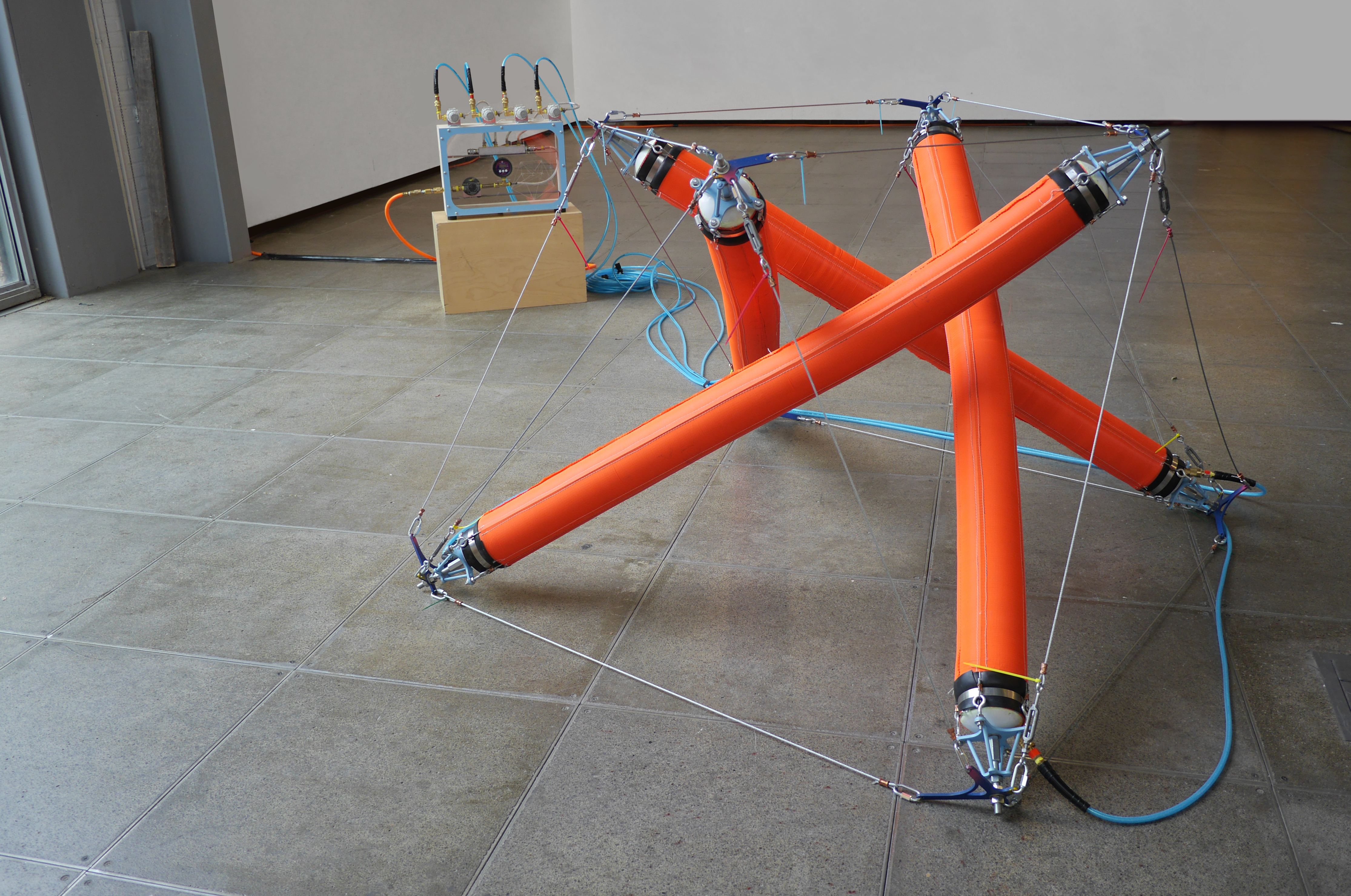
IASS 2019 Pavilion Proposal - Barcelona, Spain |
Render by Michael Koliner
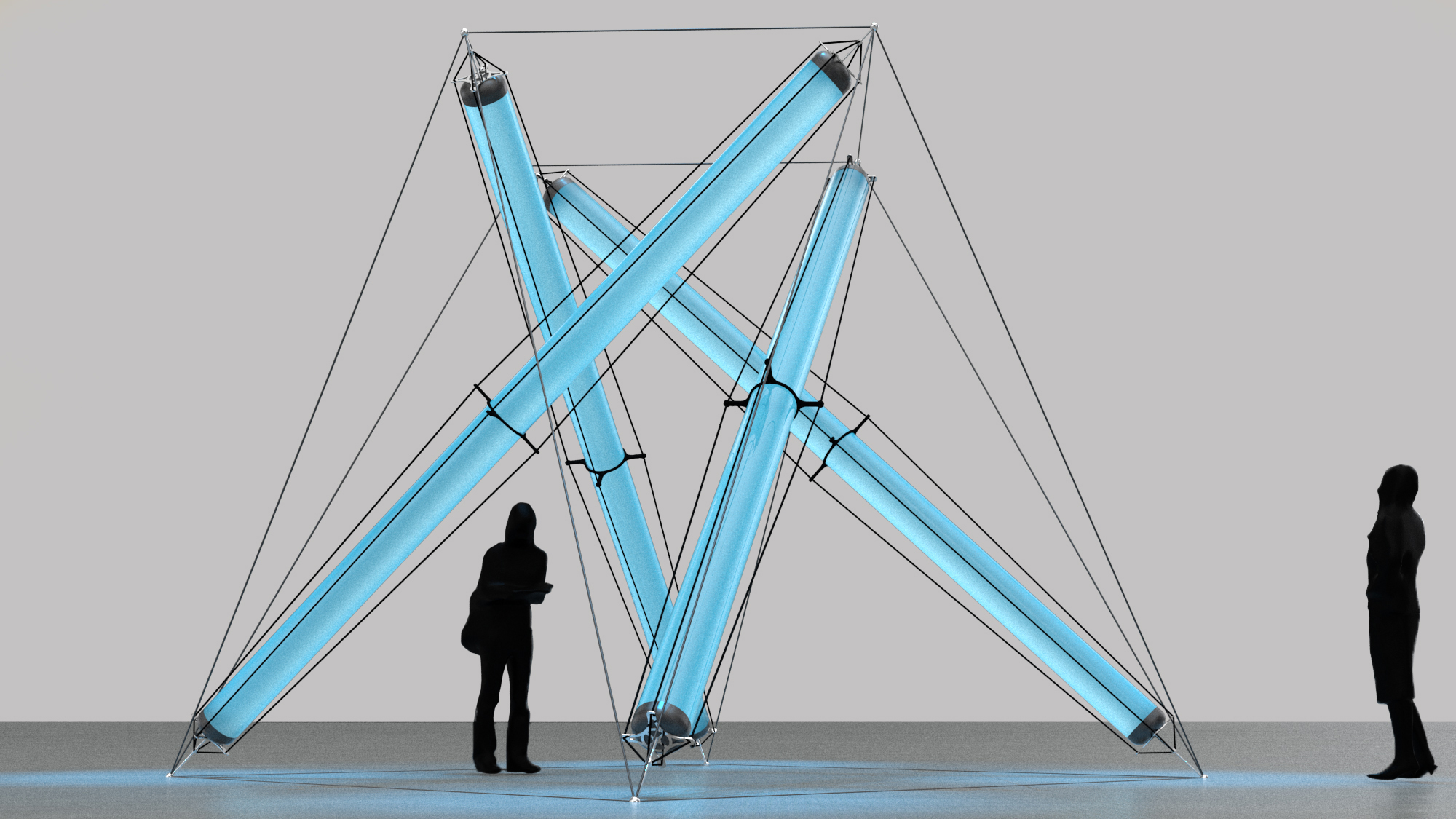
The research leading to this preliminary proposal has been centered around developing material schemas for high-performance air-struts. As the tensegrity structure is loaded, the inflated compression struts tend to deform and buckle. Our investigation has been focused on developing strategies for buckling resistance in these low-pressure struts. The inflated portion of the strut serves put a series of steel cables in tension, which provide the member with its stiffness. Through several phases of physical prototyping, we have developed several material schemas of inflatable air struts for small-scale tensegrity structures (up to 2 cubic meters) using widely available materials such as polymeric tubing, PVC pipe caps and steel cables. As this work is on-going, our team is currently developing our next experiments will lead to strategy we are proposing for the exhibition.
The proposed pavilion seeks to extend the concept of inflatable tensegrity structures by physically demonstrating it at large scale - within the spatial limits of the exhibition guidelines of 4m x 4m x 4m. The structure will demonstrate how combining the advantages of tensegrity and pneumatic structures results in a minimum weight structure that maximizes its global volume change before and after it is deployed. The design is intentionally simple: a 4-strut tensegrity geometry is used as the base form of the pavilion to demonstrate the precision of the system and the effectiveness of the low-pressure cable-stabilized struts. Whereas our previous prototypes used relatively weak plastic tubing, the struts used for the pavilion will be made of much stiffer (though still semi-transparent) membrane material. The tension cable scheme will also incorporate new strategies based on insight we gathered from recent analysis and laboratory testing. The pavilion will have integrated lighting and air-control systems in the actuating end caps of the struts; authoring them with different lighting schemes. Our submitted paper will discuss the pavilion and the numerous scale prototypes that precede it, present testing results and analytical strategies for the struts, and speculate on the range of applications for this technology.
Woven Nylon + PVC + Tension Cable Compression Strut with System - April 2019
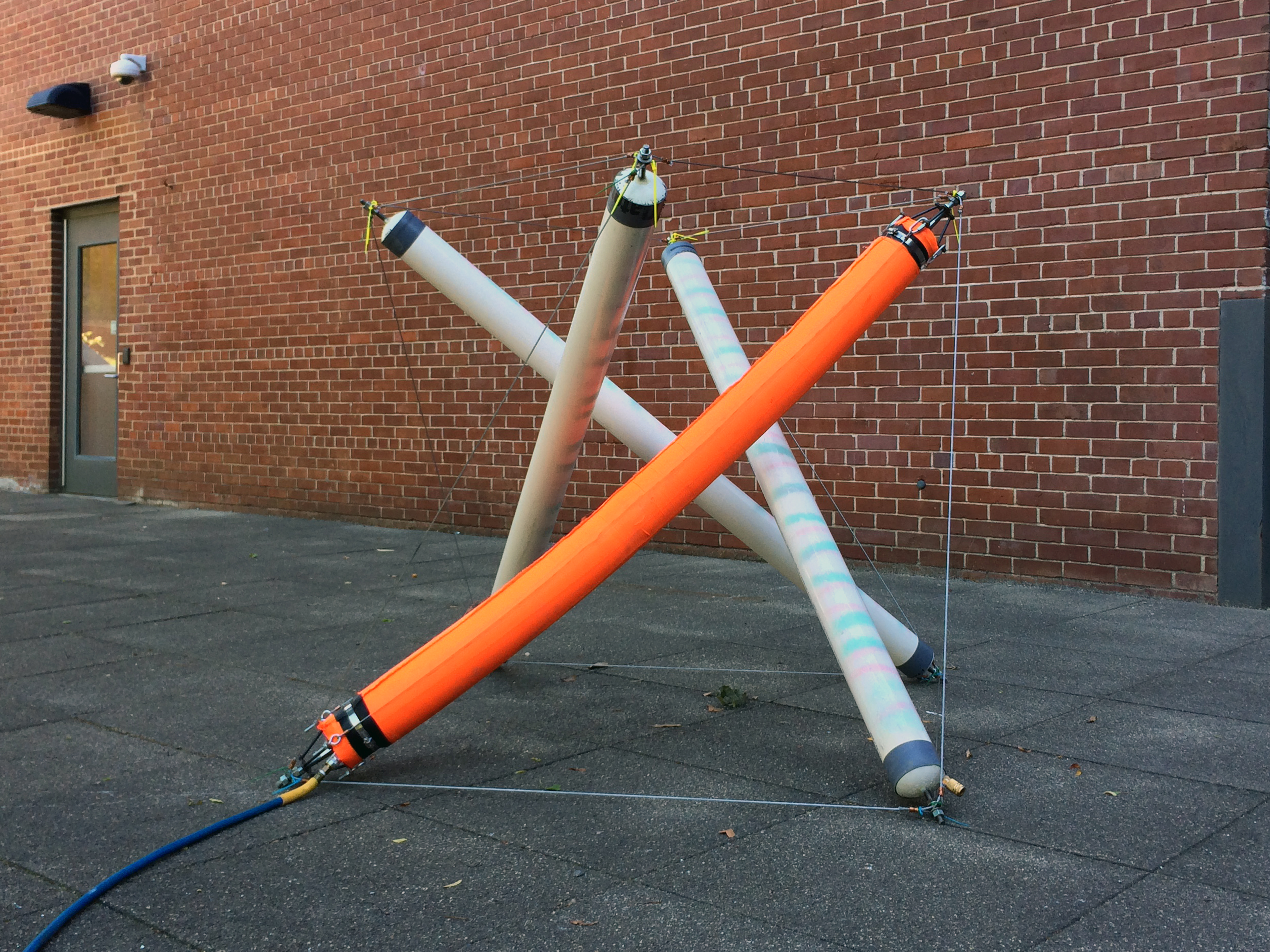

Woven Nylon + PVC + Tension Cable Compression Strut with System - April 2019
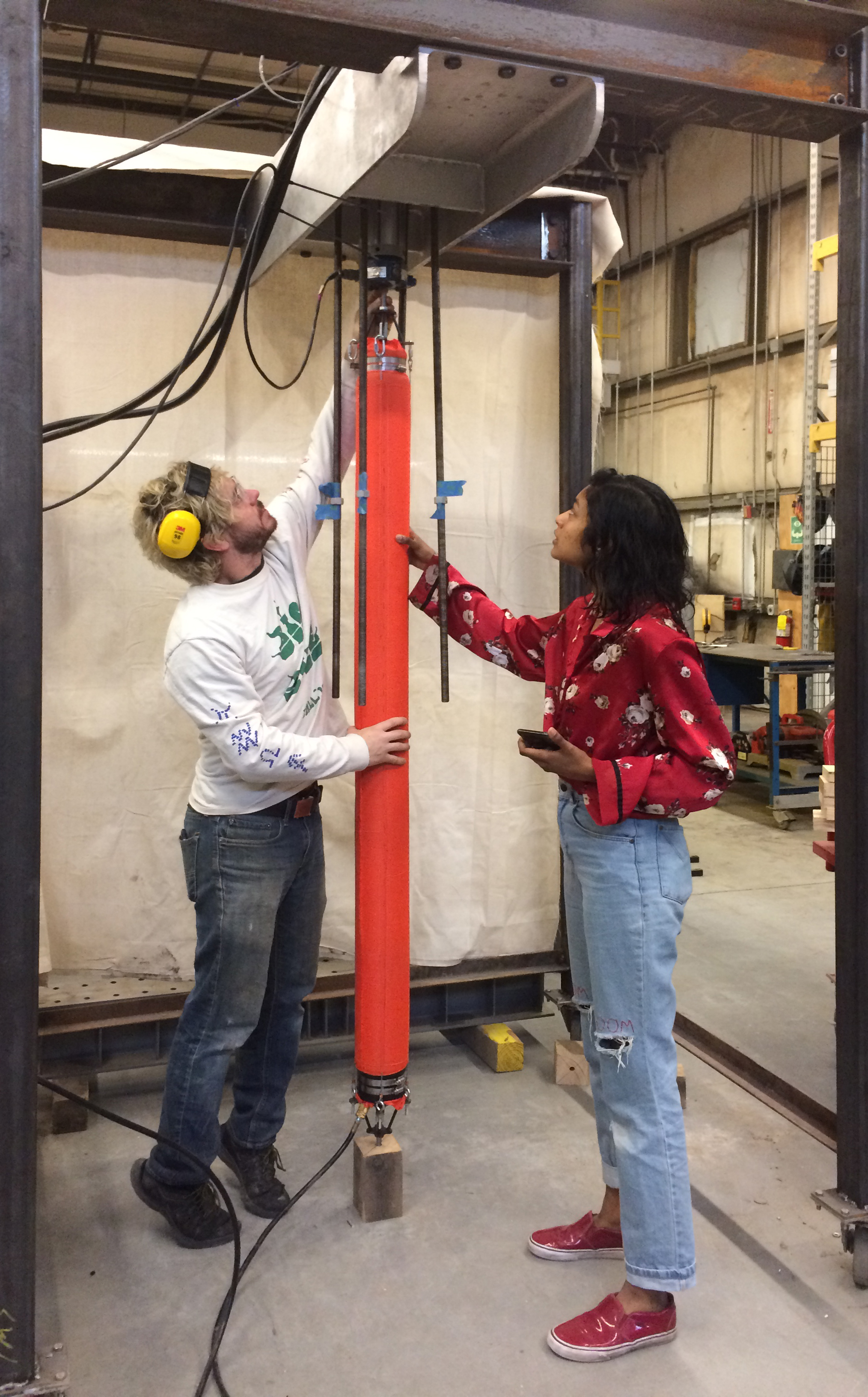

HDPE Compression Strut with Tension Cable System - December 2018

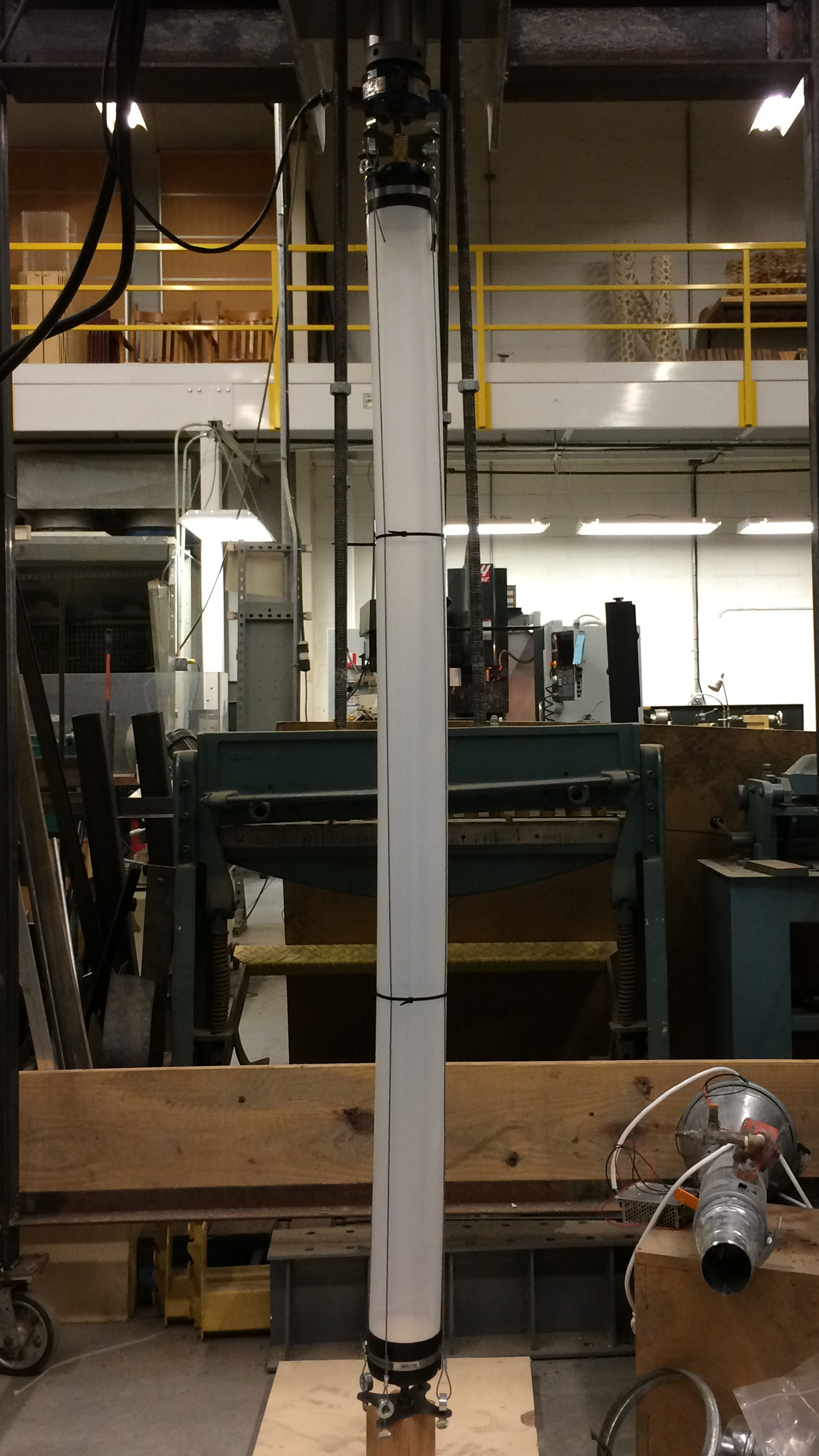
4-Strut Prototype // HDPE Membranes - October 2018



3-Strut Prototype // HDPE Membranes - September 2018



Proof of Concept Prototype // Rubber Bike Innertubes - August 2018

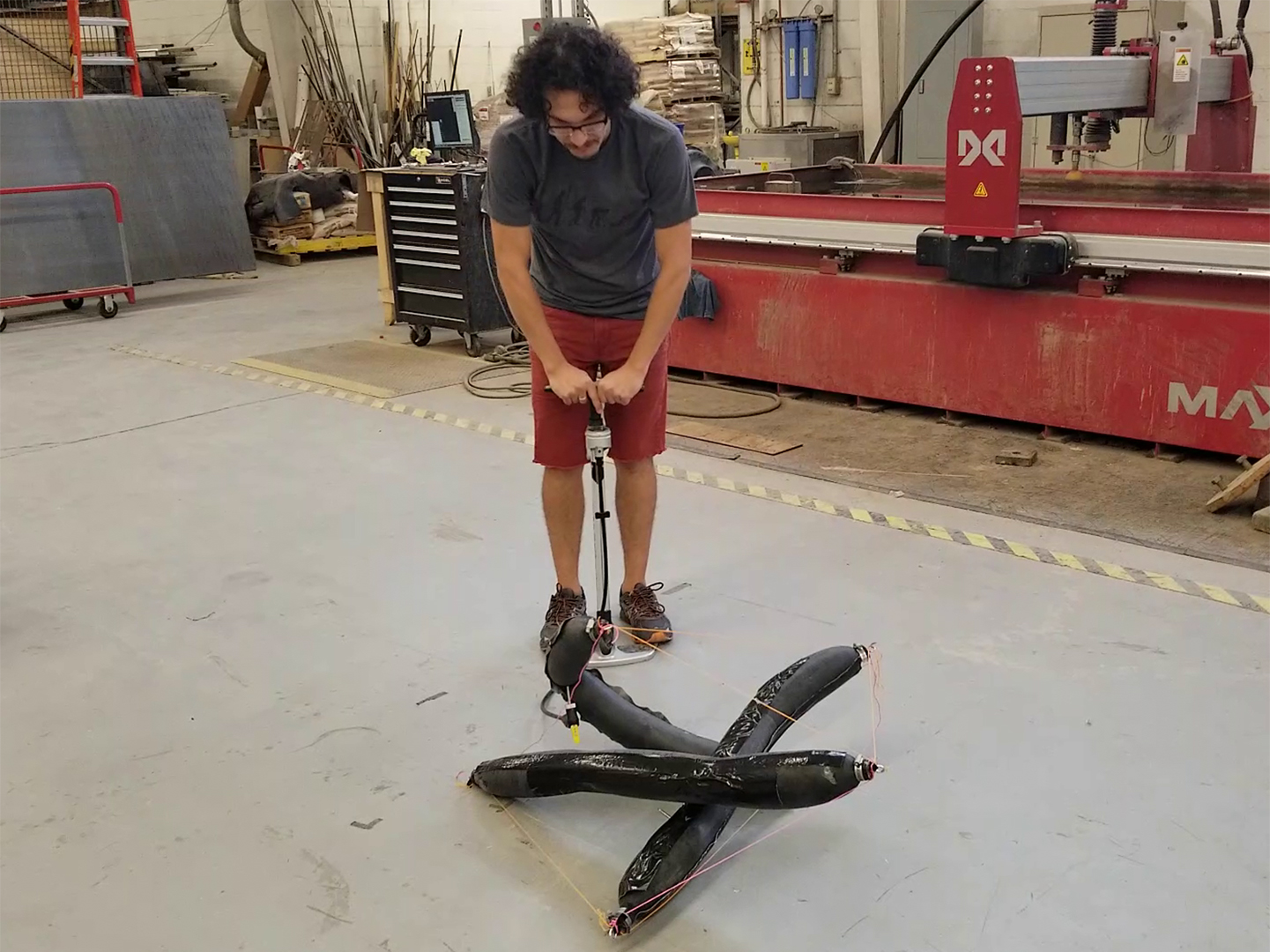

Other Projects:
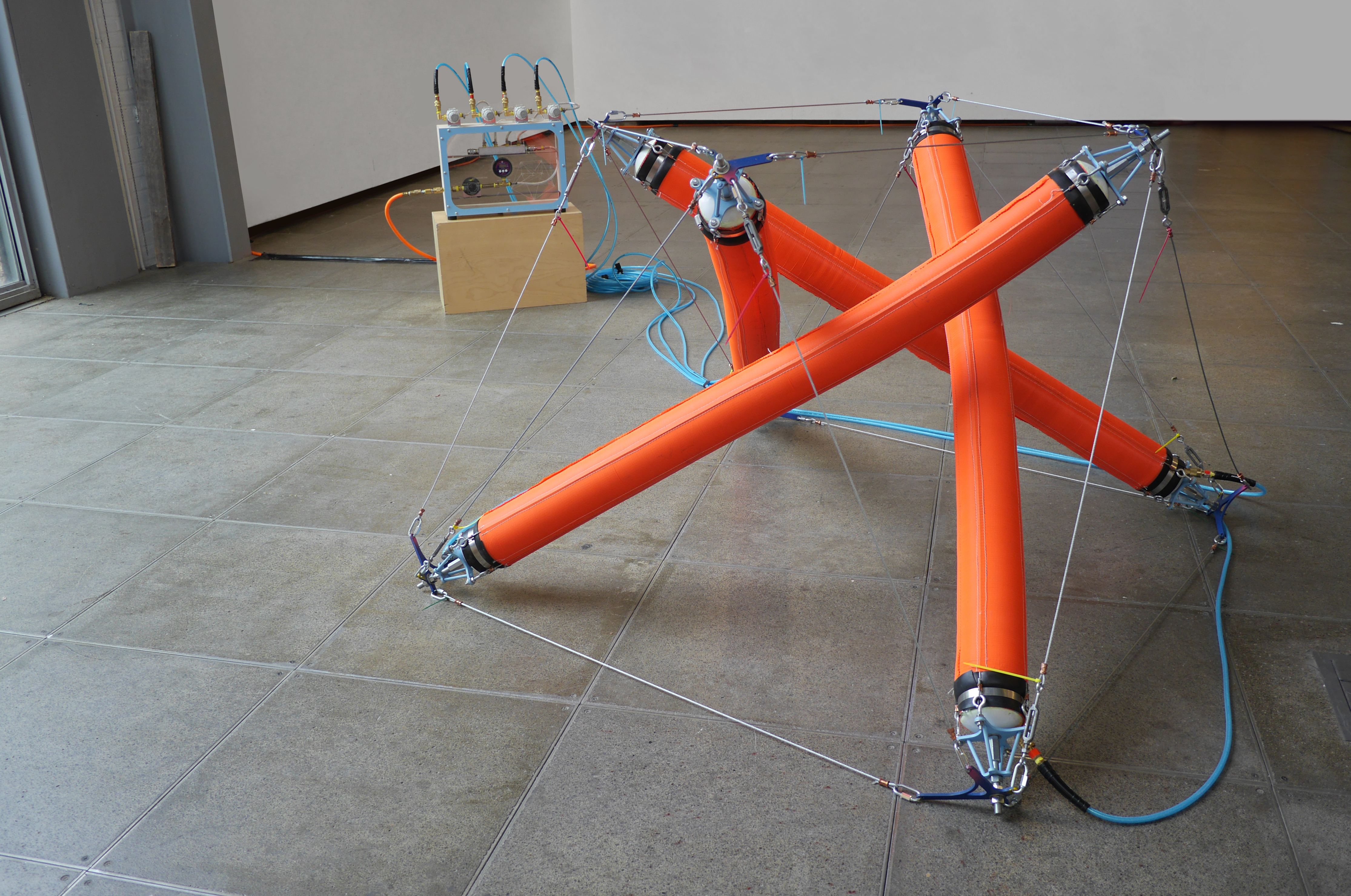